OUR CARS
PARTNER THE TEAM
CARS FOR SALE
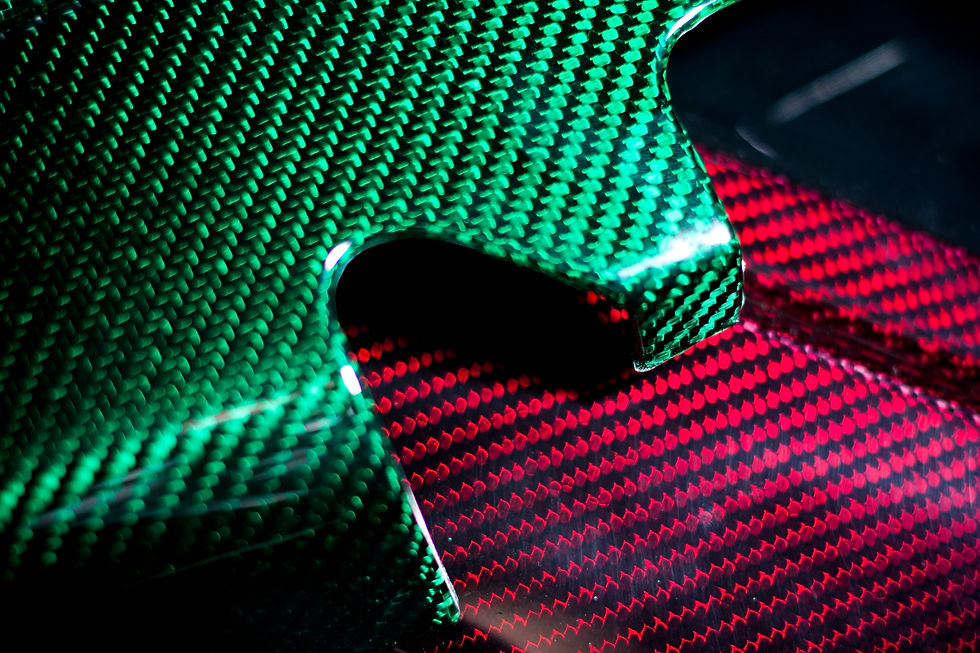


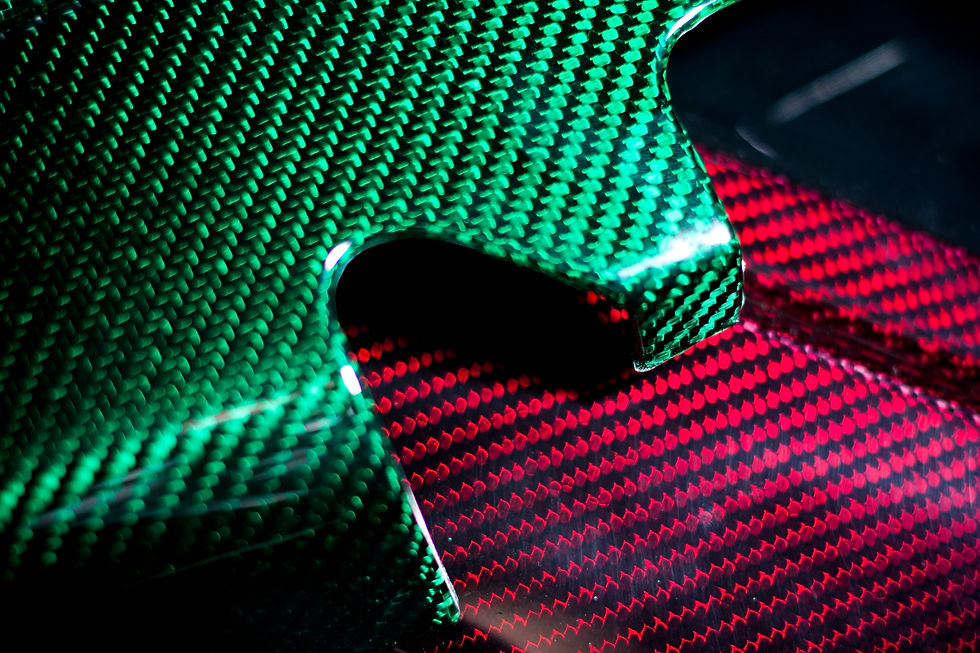
Prodrive's composites operation works within the automotive, aerospace and marine sectors producing lightweight, high performance composite components and structures. We manage the whole manufacturing process from component design and production of the tooling, to volume manufacture with CNC machine trimming with a clear coat lacquer or painted finish. We will also provide delivery and logistics support.
Find out below how Prodrive can help meet your composites requirements.
For more information contact:
Matt Bradney
T +44 (0)1295 273355
AUTOCLAVES
1.8 m ø x 4 m 200°C 7 bar
1.0 m ø x 2 m 200°C 7 bar
2.0 m ø x 4.3 m 300°C 14 bar
1.5 m ø x 2.65 m 450°C 14 bar
OVENS
3.5 m x 2.5 m x 1.5 m 200°C
2.0 m x 3.0 m x 2.0 m 200°C
0.5 m x 0.5 m x 0.5 m 250°C
CLEAN ROOMS
5 AXIS CNC MILLING
Two: 4 m x 2.6 m x 1.3 m
Component trimming
-perimeter
-critical features
Production trimming
-monolithic & cored
-foam cores
CLEAR COAT LACQUERING & PAINTING
Pattern & tooling
Components
Sand blasting
Booth size 7 m x 4 m x 2.8 m
INSPECTION
6 qualified inspectors
24/7 shift patterns
2 x faro arms
3 x CMM
A-Scan non contact NDT
OUR CAPABILITIES
MINI RRC
MINI RX
Our composite business is based in a dedicated 32,000 sq ft facility in Milton Keynes and is fully equipped with the latest composite production tools. Our team of nearly 200 engineers and technicians are fully trained in all aspects of the production process to give us ultimate flexibility.
AUTOMOTIVE
We specialise in the manufacture of AAA class finish lacquered & non-lacquered interior and exterior highly visual trim components, as well as structural components and body in black solutions with complex geometry.
AEROSPACE
We can manufacture prototype and development parts as well as tooling for development parts and early stage production. We are accredited to AS9100 and our capability extends to structures, fairings and flight surfaces and we have manufactured satellite panels and solar arrays. Today we are manufacturing the main chassis of the new European Space Agency Mars Rover.
-
Prototype & production of components & assemblies
-
Autoclave & non-autoclave processing of pre-pregs
-
Honeycomb & foam cored structures
-
Monolithic pre-preg components
-
Lean manufacturing
-
Component & tooling design
-
CNC trimming of components
-
Low cost thermoplastic components
-
Resin infusion & light RTM manufacture
-
Group synergies for procurement, inspection A-Scan NDT Laser
-
Scanning & detailed engineering design
-
Product lacquering

OUR FACILITIES

32,000 sq ft composite facility in Milton Keynes

4 autoclaves: 1.8 m ø x 4 m 200°C 7 bar 1.0 m ø x 2 m 200°C 7 bar 2.0 m ø x 4.3 m 300°C 14 bar 1.5 m ø x 2.65 m 450°C 14 bar

We have multi level clean rooms with rigorous filtration and air-lock entry
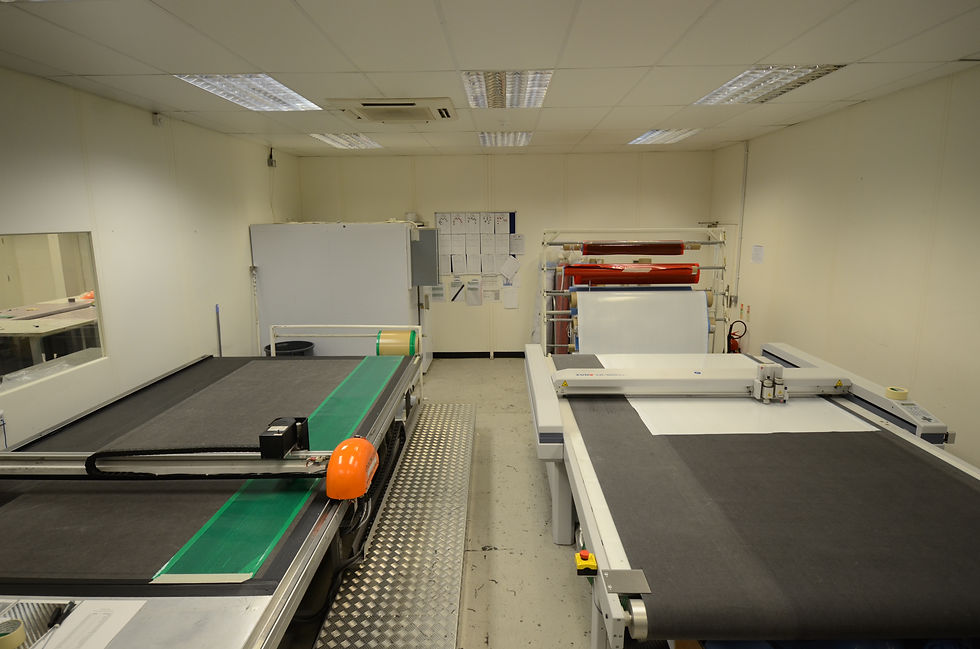
We have two automated kit cutters for pre-preg carbon sheets to minimise wastage.

Two Belotti five axis mills each: 4 m x 2.6 m x 1.3 m
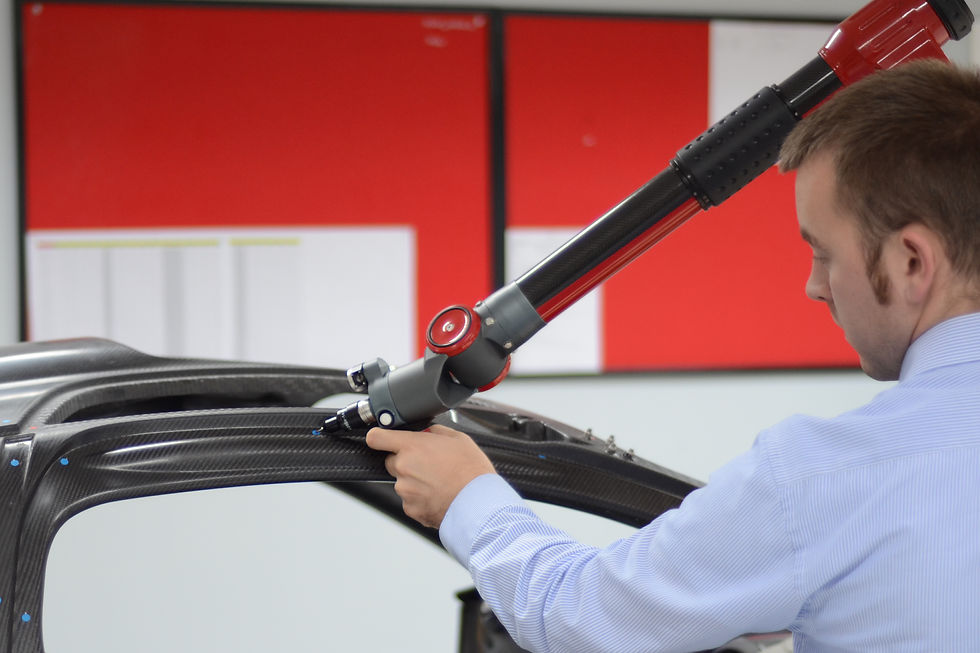
We have 3 CMMs, 2 Faro arms and A-Scan non contact NDT

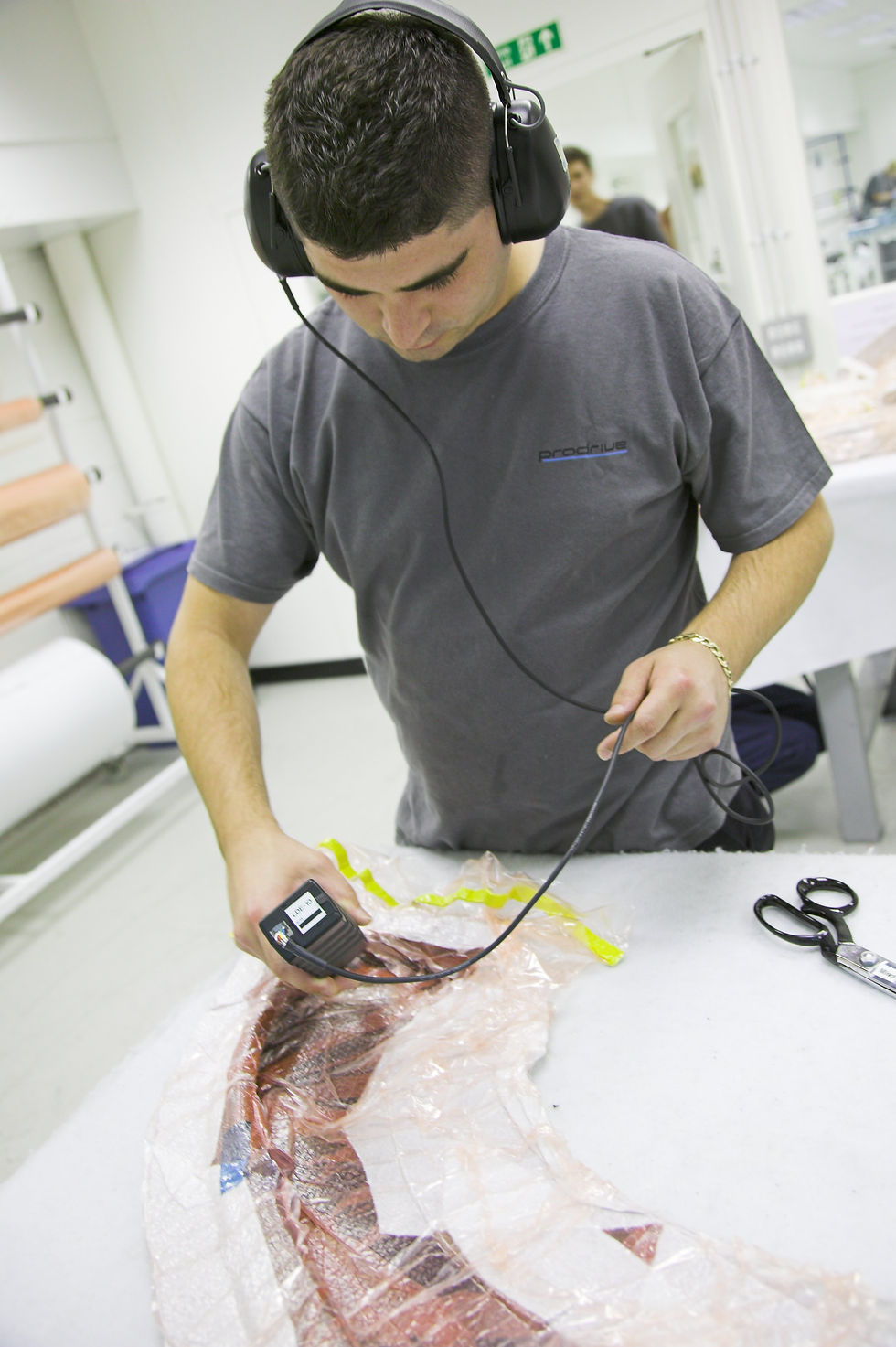

We are manufacturing the main vehicle chassis, two large instrumentation chassis and several solar panels for the European Space Agency's ExoMars programme. Prodrive is having to build the Rover to unprecedented dimensional accuracy for composites with tolerances of 20-30 microns on diameters, positional accuracy of 0.1 to 0.2 mm of features and a maximum deviation of 0.4 mm across a panel surface.
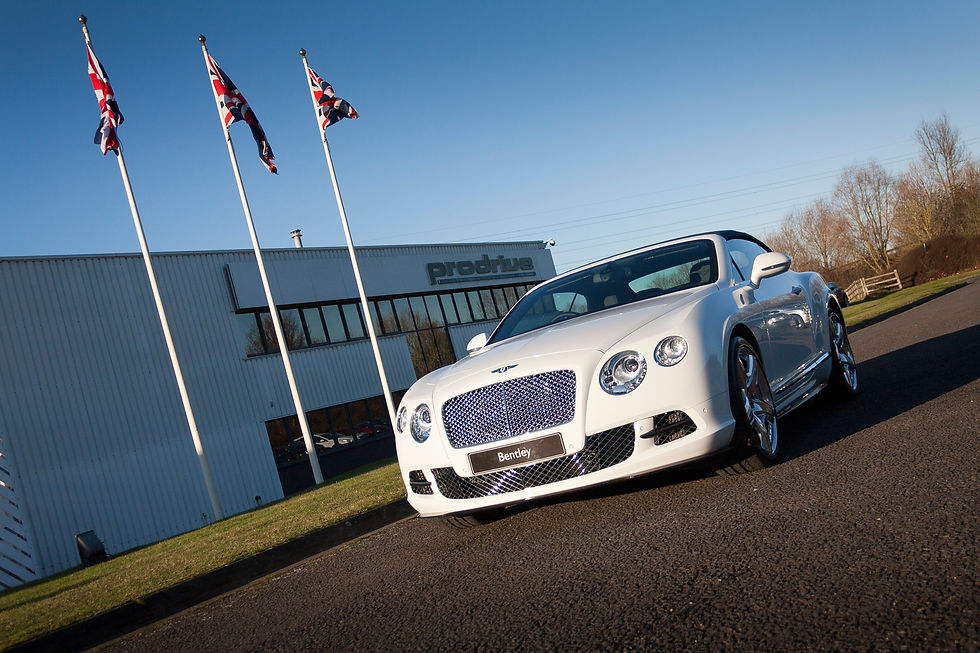
We manufacture a number of exterior and interior carbon trim components for the Bentley Continetal GT. The components are manufactured to order in Milton Keynes and delivered as required directly to the production line in Crewe. The components range from small pieces of interior trim to the largest, a rear diffuser. All have to meet Bentley's exceptionally high visual finish standards.

We manufacture the composite bodywork and interior trim for the McLaren P1. The bodywork has some of the most complex geometry of any road car while the scale of the body panels meant Prodrive had to develop special bonding processes to create the very large components. To minimise weight the interior trim remains unlacquered with a AAA rated finish requiring the utmost attention to detail in the lay-up process as the carbon weave remains visible to the owner.

We manufactured first class cabins for a leading airline for its fleet of Boeing 787 Dreamliners. A key requirement is for a very high quality finish with zero defects as the carbon wevae will be visible to the passenger.

Our new process makes carbon composite components easier to incorporate into vehicles. Features normally added in a separate operation, such as clips and inserts for threaded fasteners, can now be moulded directly on to the back of high quality composite panels, producing a more cost-effective part than a conventional bonded assembly, and one with greater mechanical strength.

We manufactured numerous lighweight panels to carry the imaging equipment on a satellite developed by the Los Alamos National Laboratory. The panels had to be manufactured in clean room conditions and had to pass strict vibration tests to replicate the conditions experienced during take-off from Cape Canaveral.
OUR WORK

We are manufacturing the main vehicle chassis, two large instrumentation chassis and several solar panels for the European Space Agency's ExoMars programme. Prodrive is having to build the Rover to unprecedented dimensional accuracy for composites with tolerances of 20-30 microns on diameters, positional accuracy of 0.1 to 0.2 mm of features and a maximum deviation of 0.4 mm across a panel surface. The Rover is being built in a special clean room facility in Milton Keynes.
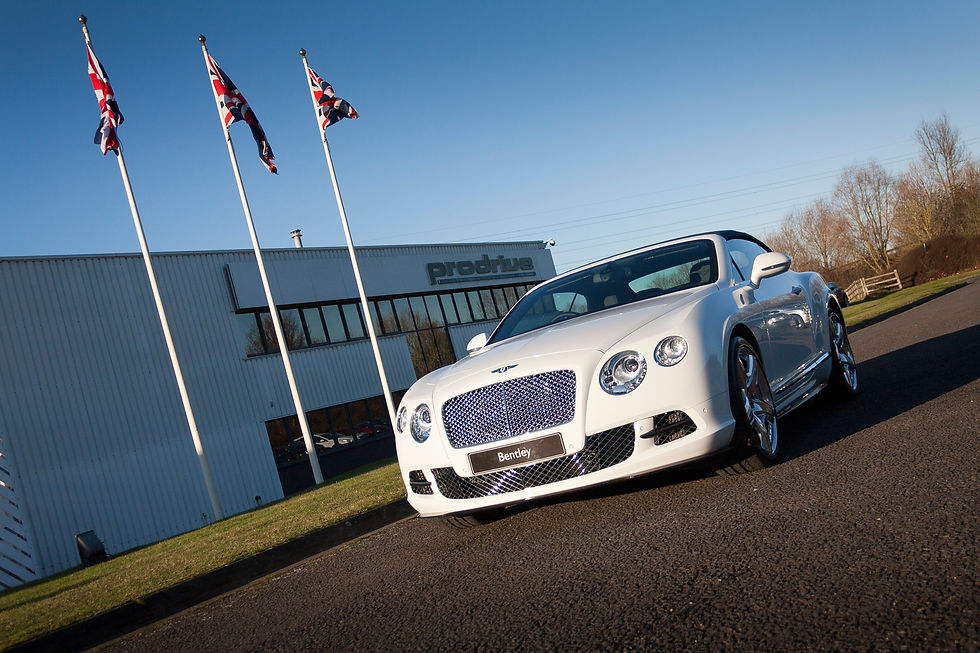
We manufacture a number of exterior and interior carbon trim components for the Bentley Continetal GT. The components are manufactured to order in Milton Keynes and delivered as required directly to the production line in Crewe. The components range from small pieces of interior trim to the largest, a rear diffuser. All have to meet Bentley's exceptionally high visual finish standards.

We manufactured numerous lighweight panels to carry the imaging equipment on a satellite developed by the Los Alamos National Laboratory. The panels had to be manufactured in clean room conditions and had to pass strict vibration tests to replicate the conditions experienced during take-off from Cape Canaveral.

We are manufacturing the main vehicle chassis, two large instrumentation chassis and several solar panels for the European Space Agency's ExoMars programme. Prodrive is having to build the Rover to unprecedented dimensional accuracy for composites with tolerances of 20-30 microns on diameters, positional accuracy of 0.1 to 0.2 mm of features and a maximum deviation of 0.4 mm across a panel surface. The Rover is being built in a special clean room facility in Milton Keynes.
neverstop
copyright Prodrive 2014
